Osmo Systems
- catherineywlee
- Jan 5
- 6 min read
Easy-to-use, real-time water quality monitoring for shrimp farms to help farmers optimize feed, reduce mortality, and decrease environmental harm
The idea
My co-founder and I were initially exploring remote sensing technology for hydroponics/aquaponics and pivoted into water quality sensing for shrimp farms as we followed demand.
One of our technical team members had discovered a novel way to combine multiple sensors (e.g. dissolved oxygen, pH, temperature, ammonia) into one. We ran a Kickstarter to build this sensor for the aquaponics space and then got into a hardware accelerator. While we were in the accelerator, the largest shrimp hatchery in Vietnam reached out to express interest. Shrimp farming wasn’t on our radar then - it’s an invisible industry to most people in the U.S. because the U.S. farms a negligible amount of shrimp. When we visited Vietnam, we saw the scale of aquaculture and the size of the opportunity. Shrimp is one of the highest revenue-generating ocean products globally but has much higher mortality rates than other commonly consumed protein sources like chicken, and there is very little technology customized for their operations.
When comparing the highest shrimp-producing nations, we found that farms in SE Asia tended to have very small footprints, whereas Ecuador had much larger and longer ponds where they grew shrimp at a lower density. To increase density they would need more tech. So even though our initial relationships were with farmers in Vietnam and Thailand, we planned our product release in Ecuador due to a more favorable structure for selling sensors (plus a better time zone and flights!)
Our all-in-one sensor was exciting to prospective customers because it had the potential to provide multiple data points at a lower price point (e.g. standalone ammonia sensors are super expensive). We wanted to make a cheap enough sensor so that you could leave them in the fish ponds and replace them each month rather than having to re-use and recalibrate them. We would have a wireless system that connects the sensor data to a home unit, and you could monitor water quality to prevent sudden-death of a whole pond - the biggest concern farmers faced. Measuring dissolved oxygen levels is important because shrimp need to breathe oxygen from the water and if available oxygen is depleted (e.g. from algae blooms) the whole crop can die overnight. We charged a fee for the sensor device and a monthly fee for software and sensor cartridges. Our long-term vision was to expand beyond water quality monitoring into automating other processes for shrimp farmers such as measuring, counting, and feeding shrimp.
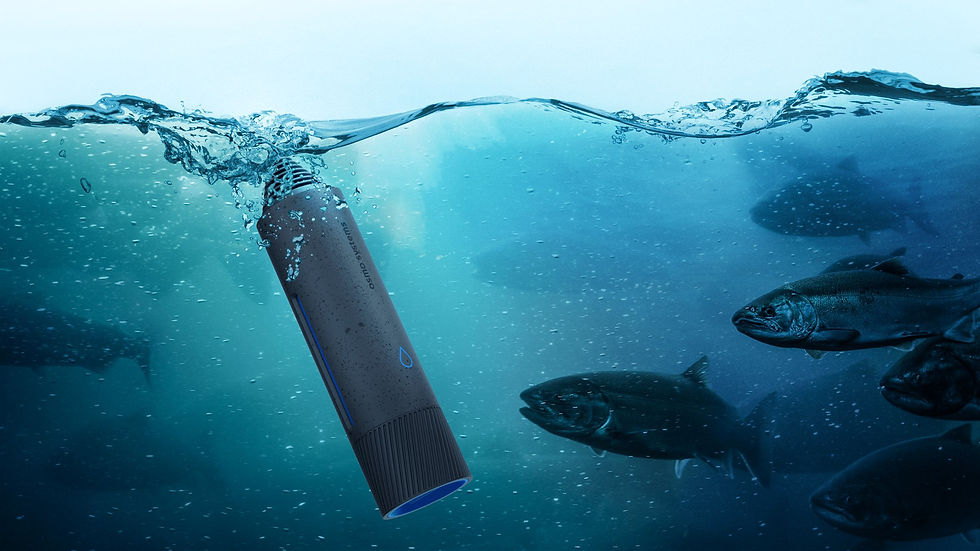
Competitors / Substitutes
Various standalone sensors were being provided by different companies. There were companies in China working on wirelessly connected sensors for pH, but they focused on solving connectivity rather than innovating on the biofilm side like we were. After we closed, we also learned about a bigger competitor that was working on a way to make sensors that didn’t touch the pond water so that they would not be affected by biofilm (a big issue we encountered).
Amount raised
Raised ~$2M at seed. With follow-on investments, we’d raised a total ~$4M before shutting down.
Duration
End of 2015 to end of 2019
Team size
10 at peak
What went well
There was clear demand for the product. There were so few resources going into solving the problems in shrimp farming that even with relatively little expertise/notoriety, our team was being flown out to shrimp farms in SE Asia and contacted by the largest Asian food manufacturers for our product. A lot of folks were willing to write LOIs and accept our proposed pricing. But this was all based on the assumption that our product worked as we designed it.
Challenges and what you'd do differently
Technical issues
We did not end up building a sensor that worked as we envisioned. Our product was designed on three premises: 1) it does not require a high skill level to operate (it would be self-calibrating), 2) it would be inexpensive, and 3) you could leave the sensor in water 24/7 for constant monitoring.
The biggest challenge was that we had to make these sensors inexpensive AND be able to work in shitty (literally!) water conditions. We wanted to be able to leave a sensor in the shrimp pond for at least a month, but ponds are really dirty with food particles, algae, and excrement. We tested our sensors in the lab in clear water. In actual conditions, biofilm collects on the sensors in the water and affects readings. Variations in water quality had a huge impact on results.
We spent our first year post-fundraise getting a prototype ready for in-field testing. We used a single LED sensor with a photo-sensitive material (“patches”) in the cartridge. When you shine a light on the material to excite it, the concentration of dissolved oxygen or ammonia in the water will result in a different light color (i.e., the fluorescence was less bright when there was more dissolved oxygen). In time, we realized this wouldn’t work beyond a proof of concept - we could show it responding, but not with the consistency we needed. We could not make a whole fleet of sensors that were accurate to each other. So, we had to move away from the light sensor idea.
We went back to the drawing board to try a secondary approach for a year. We used a cell phone camera that allowed us to look at the whole area of all the patches at once (so we could count the Dissolved Oxygen patch and its reference patch, the Ammonia patch, and its reference patch, and compare each of those to each other) which solved the calibration and manufacturing issue that we encountered with our first light sensor. BUT this did not solve our biggest problem - the biofilms that occur in real-world shrimp ponds.

We also recognized other technical issues would be coming down the pipeline, such as the way suppliers manufactured their coating, where the concentration of photoactive material differed from the middle vs. the end of the strip. We would have to work with manufacturers to change how they were making it. Also, how would we get power to the sensor? Most shrimp ponds are not electrified. We considered building a big buoy around the sensor (so it would not get lost) and adding a solar battery - the ideas got comical at one point! Notably, these were not unsolvable problems, though. It’s common that in making sensors we make many of them and bin (grade) them by different levels of accuracy. It would just take time, and we didn’t get to that point.
By the time we tested our second prototype in actual shrimp ponds, we had a few months runway left and were preparing to raise more. We hadn’t solved the biofilm issue yet and were considering ways to prevent the sensor from sitting in the water, maybe just dipping it periodically. Investors were willing to give us more money, but we knew we had to go back to experiment further, and we were burnt out, so we decided to shut down operations.
Focus vs. Pivot
One thing I might have done differently is not being locked in on solving water quality, and being open to solving a different problem for the shrimp farmers that was quicker to build and could have paid for continued development of other technology. We knew that shrimp farms were underserved and had such little technology. Because we had started with this novel approach to water quality monitoring and were seeing technological success initially, we were fixated on solving that problem. It’s not clear we actually had to tackle that problem first. But we had sold investors and ourselves on it! We may have been able to look at the broader set of issues and get the farmers something easier to build, like an automated feeding basket and/or shrimp counter using objective recognition, that would have funded future work.
Team growth and spend
We hired a bunch of technical and business people too early and were too late to let people go. Once we raised, there was pressure to spend. My co-founder was doing a great job keeping business leads alive while I was pushing on the technical front, so we really didn’t need more business people to expand relationships until we had a product farther along. And once you bring someone on the team you feel committed to working on the idea that we hired them for. It contributed to feeling locked into the water quality monitoring solution. I think keeping a leaner team would have given us more flexibility. We also spent money on industrial product design with beautiful images and branding - but realistically, our shrimp farm customers don’t care about that; the materials were really for VCs.
Interview above with Osmo Systems co-founder / CTO James Regulinski. James now runs Carbon Collective, an online-only investor advisor that helps put your retirement fund to work fighting climate change. For more details on the software and hardware design for Osmo System’s sensors, check out this case study by one of the team members.
Comments